碳化硅在冶金行业的应用全解析——从脱氧增效到风险规避的实战指南
碳化硅(SiC)作为冶金行业的关键材料,凭借其耐高温、高硬度、抗氧化等特性,已成为炼钢、铸造、耐火材料等领域的“隐形守护者”。金钢供应链将结合行业数据和实战案例,详解碳化硅的核心应用场景、使用方法及风险防控策略。
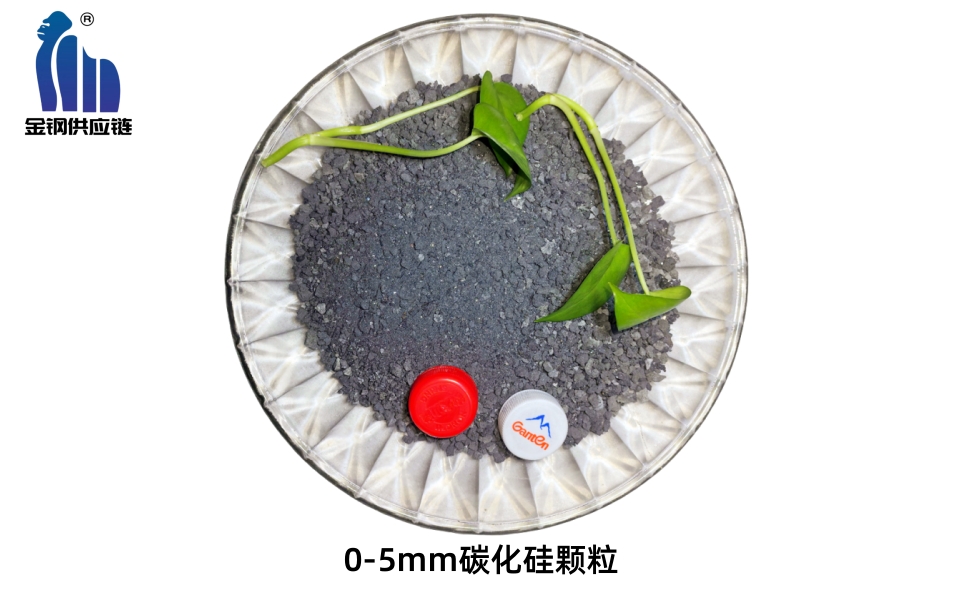
一、碳化硅在冶金行业的三大核心应用
1. 高效复合脱氧剂:炼钢工艺的“净化器”
碳化硅脱氧剂(SiC≥70%)通过以下机理提升钢水纯净度:
双重脱氧机制:碳化硅分解生成的SiO₂和CO气体,与钢水中的游离氧结合,形成低熔点炉渣上浮。例如某钢厂使用碳化硅替代传统铝脱氧剂,脱氧效率提升40%,吨钢成本节省18元。
节能降耗:碳化硅脱氧可降低电耗5%-8%,并提高锰、铬等合金元素的回收率(如锰回收率从82%提升至90%)。
环保优势:相比硅铁脱氧,碳化硅减少粉尘排放30%,且炉渣量减少15%。
添加标准:
炼钢脱氧:推荐添加量0.3%-0.8%(视钢种调整),粒度10-50mm自然块;
炉外精炼:采用0.2-1mm细粉,添加量0.1%-0.3%,通过喂丝机精准投料。
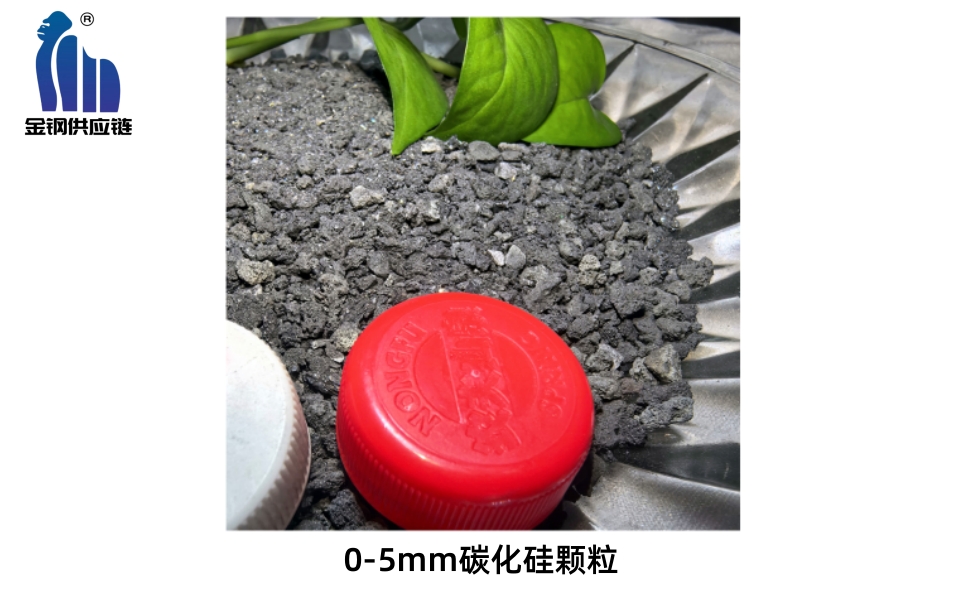
2. 铸造孕育剂:消除白口、提升铸件性能的“催化剂”
在灰铸铁、球墨铸铁生产中,碳化硅孕育剂(粒度0.2-8mm)通过以下方式优化铸件质量:
石墨形态控制:促进A型石墨生成比例达85%以上,减少D型石墨导致的脆性问题;
消除白口缺陷:薄壁铸件白口率从12%降至1.5%,特别适用于汽车制动盘、发动机缸体等精密铸件;
提升加工性能:铸件表面硬度均匀性提升30%,车削刀具寿命延长2倍。
应用技巧:
添加时机:铁水温度1450-1500℃时,随流加入浇包;
添加量:灰铸铁0.2%-0.6%,球铁0.1%-0.4%,超量易导致缩松缺陷。
3. 耐火材料与耐磨部件:高温设备的“铠甲”
碳化硅凭借2715℃的熔点和优异热稳定性,广泛应用于冶金设备:
耐火内衬:电弧炉炉壁、钢包渣线部位采用Si₃N₄结合碳化硅砖,寿命提升3-5倍;
轧钢耐磨件:碳化硅陶瓷轧辊比传统合金辊耐磨性提高8倍,减少停机更换频率;
高温传感器保护套:在1600℃环境下连续工作超5000小时,保障数据采集稳定性。

二、碳化硅在冶金中的使用要点
1. 粒度选择与预处理
炼钢脱氧:10-50mm块状,减少氧化烧损;
铸造孕育:0.2-3mm雾化粉,需预热至200-300℃去除吸附水;
耐火材料:骨料粒径分级(如1-3mm、3-5mm),搭配细粉提升烧结密度。
2. 温度与工艺协同控制
炼钢脱氧温度控制在1580-1650℃,避免低温导致碳化硅未完全反应;
铸造孕育时,铁水过热度应≥100℃,防止孕育衰退。
3. 复合应用增效方案
硅铁+碳化硅:按7:3比例复合脱氧,兼顾反应速度与成本;
碳化硅+稀土镁:用于球铁生产,石墨球化率提升至90%以上。
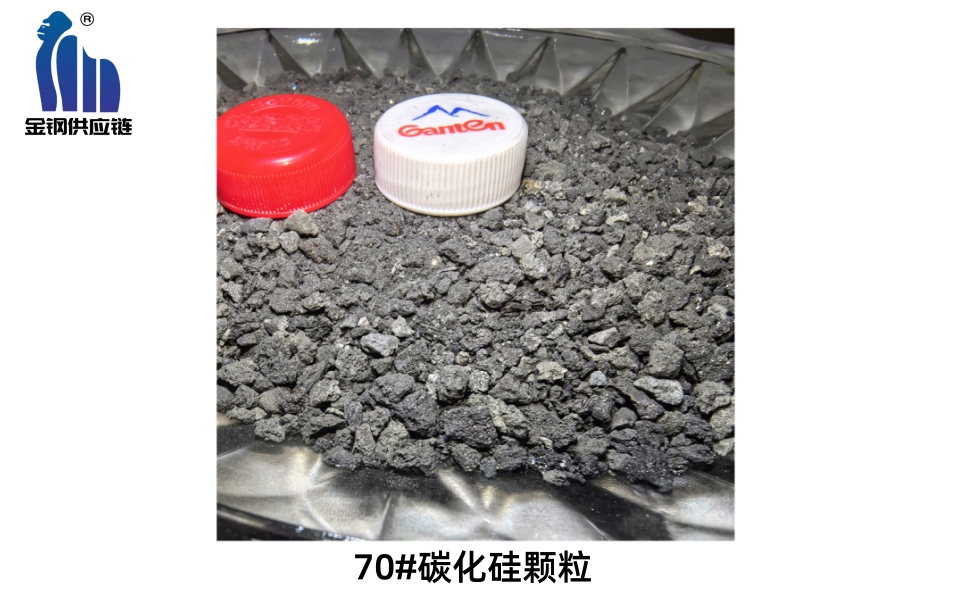
三、劣质碳化硅的五大风险与防控策略
1. 成分虚标引发质量事故
风险点:SiC含量不足(如标称70%实际仅60%),导致脱氧不彻底、铸件气孔率激增;
防控措施:要求供应商提供第三方检测报告,重点核查SiC、游离碳指标。
2. 杂质超标损害设备
风险点:Fe₂O₃、Al₂O₃等杂质超限(如>3%),加速耐火材料侵蚀;
案例:某钢厂因使用高铝碳化硅(Al₂O₃ 5.2%),钢包寿命从80炉次骤降至45炉次。
3. 粒度不均影响工艺稳定性
风险点:粉末占比>15%的块状料,导致脱氧反应剧烈喷溅;
解决方案:采用激光粒度仪抽检,要求粒度合格率≥95%。
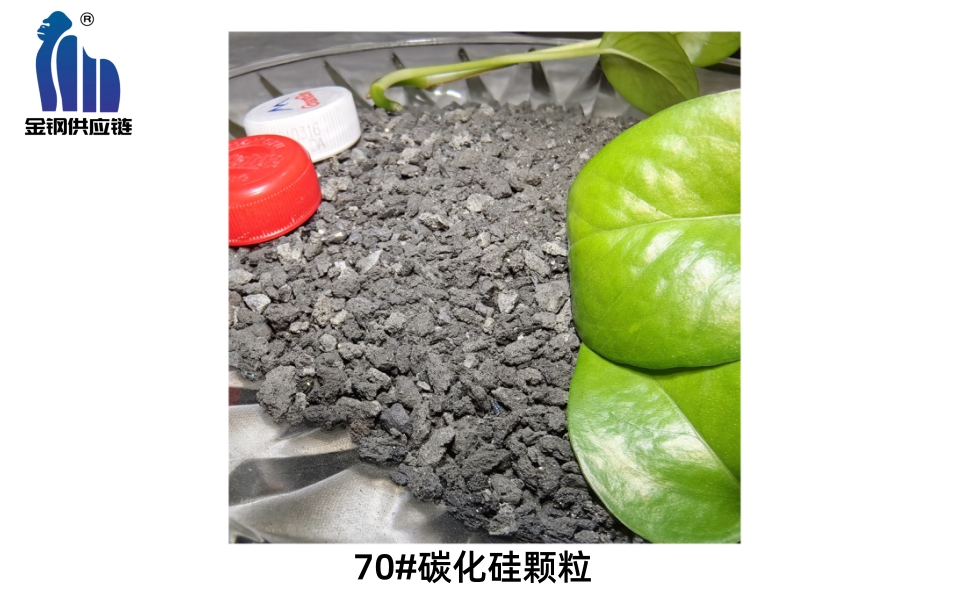
四、采购与使用建议
1. 优选源头厂家:实地考察年产万吨级企业,查验矿热炉(≥12500kVA)等核心设备;
2. 签订质量协议:明确SiC≥70%、粒度偏差±5%等条款,设定超标赔付机制;
3. 建立应用数据库:记录不同批次碳化硅的脱氧效率、铸件良品率等数据,优化添加方案。
结语:碳化硅应用的“黄金法则”——精准匹配工艺需求
冶金企业应建立碳化硅全生命周期管理体系,从采购验收到工艺适配形成闭环。