碳化硅在冶金工业的应用与技术指南
一、核心应用场景与技术原理
1. 高效复合脱氧剂
定义:碳化硅(SiC)作为炼钢脱氧剂,通过硅、碳元素协同作用降低钢液氧含量,替代传统硅铁、锰铁等金属脱氧剂。
技术突破:
脱氧效率提升30-50%,降低电耗5-8%(某钢厂数据)。
形成SiO₂-MgO-Al₂O₃复合脱氧产物,减少夹杂物尺寸至3μm以下。
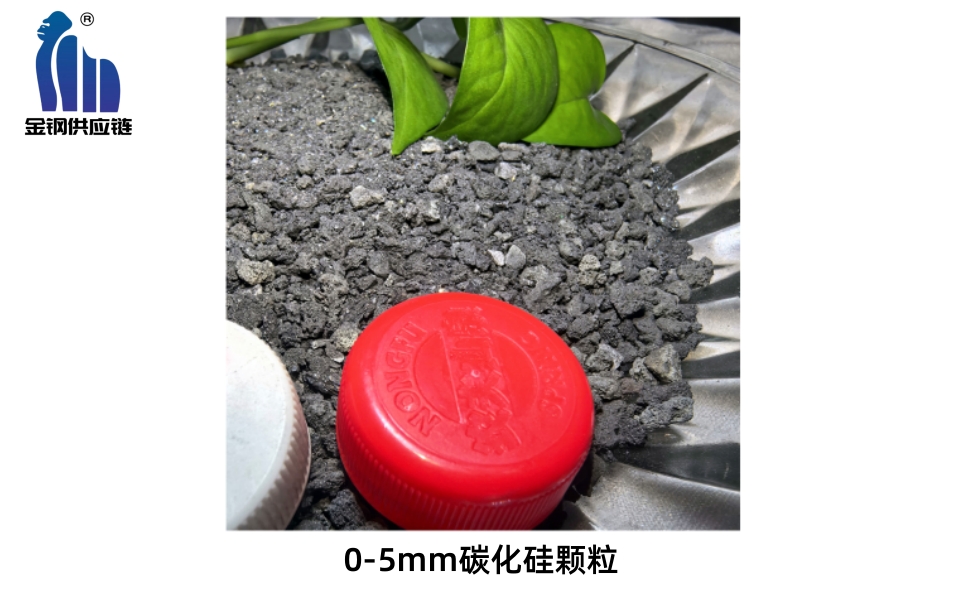
争议点:
高纯度碳化硅(SiC≥98%)成本较高,部分企业倾向采用冶金级碳化硅(SiC 80-90%)。
碳元素残留控制难题:需配合动态氧含量检测系统(争议焦点:在线监测设备投资回报率)。
2. 高温耐火材料
定义:利用碳化硅高熔点(2700℃)、低热膨胀系数(4.5×10⁻⁶/K)特性制造的炉衬、轧辊等高温部件。
行业趋势:
2024年电弧炉用碳化硅耐火材料市场规模达$1.2B,CAGR 6.8%(QYResearch)。
新型纳米碳化硅-氧化锆复合材料提升抗热震性200%。
技术瓶颈:
碳化硅与金属界面结合强度不足(解决方案:梯度复合涂层技术)。
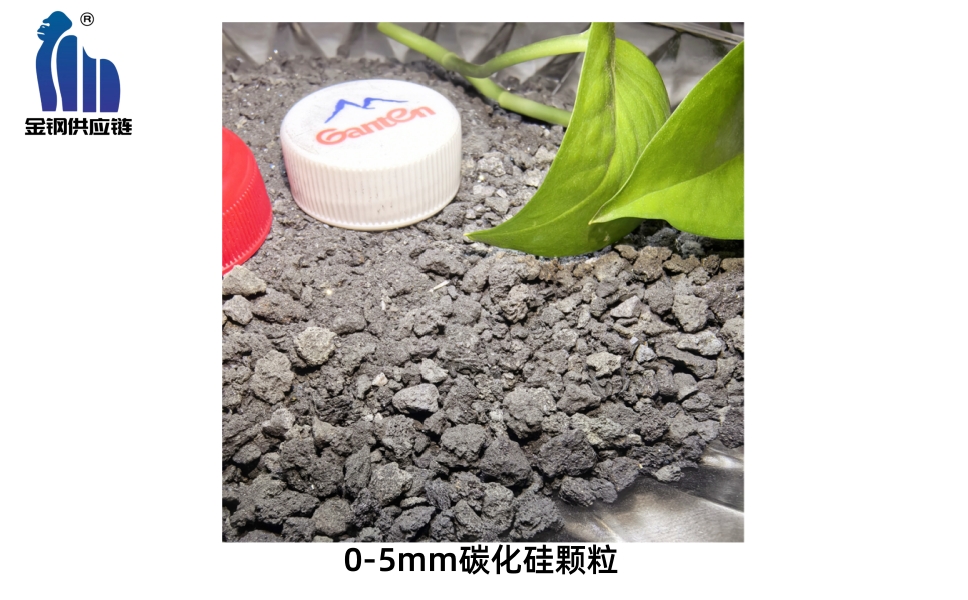
环保压力:传统碳化硅生产能耗达3000kWh/吨(行业转向微波烧结工艺)。
3. 铸铁冶金改良剂
定义:通过碳化硅的形核作用优化铸铁石墨形态,提升力学性能。
实证数据:
灰铸铁抗拉强度提升15-20%(ASTM A48标准验证)。
球墨铸铁球化率从85%增至92%(某汽车铸件厂案例)。
操作争议:
预处理温度窗口:1450-1520℃(传统派主张固定温度VS革新派主张动态温控)。
粒度选择:0.3-1mm(占70%市场)与纳米级碳化硅(成本溢价300%)的效益之争。
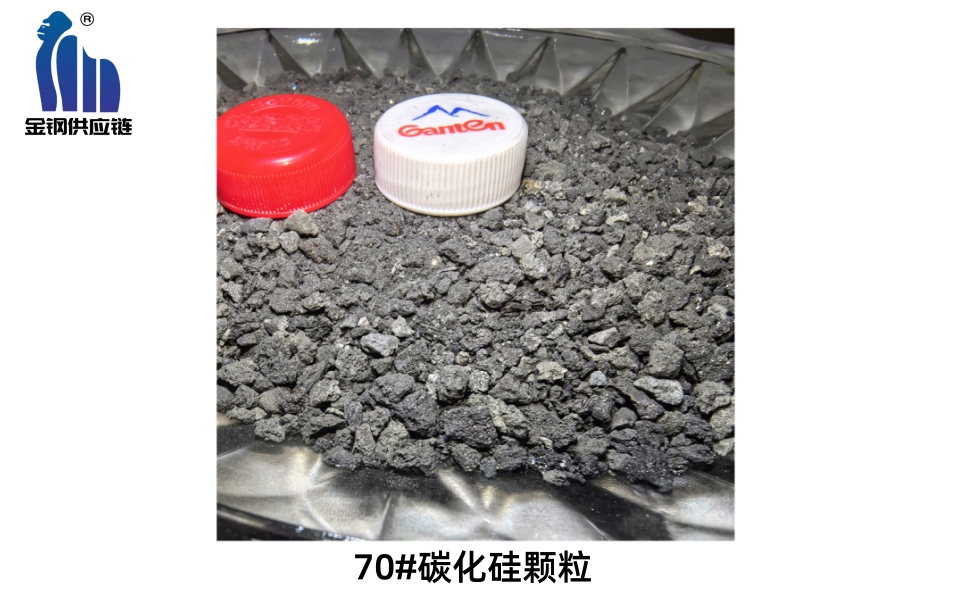
二、应用技术参数与操作规范
1. 添加比例基准
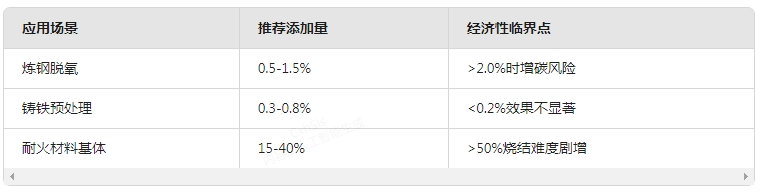
2. 工艺控制要点
粒度匹配:炼钢用1-3mm(过细则烧损)、铸造用0.5-1mm。
时序控制:电弧炉应在熔清后15分钟内加入(氧活度0.002-0.005时最佳)。
成本优化:混用30%再生碳化硅(破碎料)可降本18%。
三、技术经济性对比
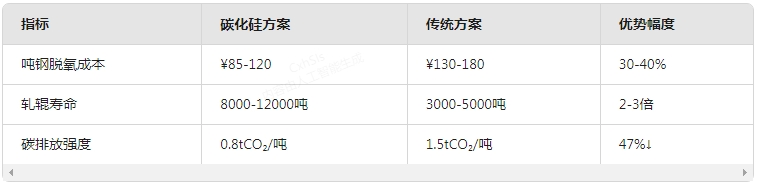
四、智能总结(5点核心洞察)
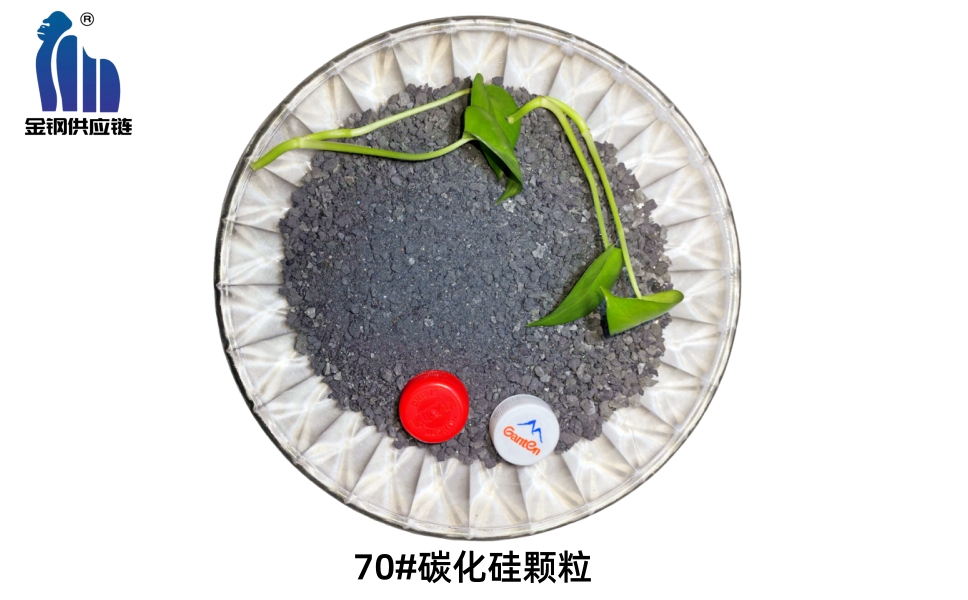
1. 脱氧革命:碳化硅脱氧剂使炼钢综合成本下降20%,但需配套动态氧控系统。
2. 材料突破:纳米碳化硅复合材料将耐火材料寿命推至万炉级,但微波烧结设备投资回收期需5-7年。
3. 铸铁升级:0.5%碳化硅添加使发动机缸体废品率从8%降至2%,但需严格控温±15℃。
4. 循环经济:再生碳化硅应用可降本20%,但需建立粒径分级体系。
5. 技术路线:2025年冶金级碳化硅市场将分化——高端应用追求98%纯度,普钢领域接受85%经济型产品。